The production process of lithium battery production line, and will it cause (gas, water and soil) pollution during the process? At the current stage of the production process of lithium batteries, lithium batteries (Li-ion) will not be polluted by (toxic heavy metals).
1. Start with the battery itself
Of course, this concept is relative, and lead-acid, nickel-chromium batteries, its pollution is very small, there is no heavy metal pollution. But for the environment, it is definitely harmful (what is chemical not poisonous?).
It needs to be explained again that compared with traditional batteries, the pollution is extremely low.
2. Let's talk about the pollution that may occur in the process of producing batteries. (Picture taken from Lithium-ion batteries: A Japanese tech growth story?)
The pole piece production process: In these processes, the domestic mainstream lithium iron phosphate system, or even the ternary system, does not have relatively large pollution. Of course, the ternary system may still have some pollution with lithium cobalt oxide. Yes, for example, cobalt, manganese, and nickel are all heavy metals, but they are relatively environmentally friendly. Among them, lithium iron phosphate is the most environmentally friendly. The remaining part, except for the pollution of the materials mentioned above, the solvent in the injection is mainly cyclic/chain carbonate or carboxylic acid ester. The solute is mainly lithium salt lithium hexafluorophosphate, and the additives are mainly film-forming additives, flame retardant additives, conductive additives, and additives to improve low-temperature discharge. The pollution in the whole process is okay. Of course, chemical agents, if you don't pay attention to their control, will definitely pollute the environment. As for the final packaging and formation, the pollution is even smaller. The different production methods shown in the figure are as follows:

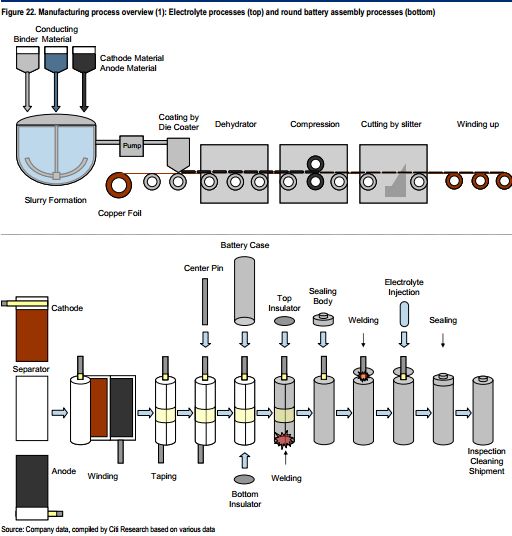
The recovered metals value from a collected recycled battery is enough to justify recycling
The government mandates that you recycle the battery
The second reason is the simplest and is most exemplified in lithium batteries by the EU Battery Directive, which mandates a certain level of collection and a recycling percentage for every battery sold, although there are many other batteries covered by it. The most common reason is not actually recycling qua recycling but environmental protection. The most frequently recycled battery in the world is the lead-acid battery used in car starters, simply because in most developed countries there are very strict controls on the lifecycle of products made from lead. Similarly, there is a very high rate of recycling of nickel-cadmium (NiCd) batteries for similar environmental protection reasons.
The first reason is more complicated, and has an inherent chicken-and-egg problem when it comes to lithium batteries in particular. That problem is collection, also known as reverse logistics.
Reverse logistics is the way recycling companies get their feedstock. However, it doesn’t exist in a vacuum. Gathering batteries at end-of-life is an expensive prospect in and of itself; they are inherently distributed, even in areas with high population density like urban areas, and it’s hard to build the infrastructure to convince people to discard them separately. In order for such a service to work, it either has to be run by the government, or it has to receive payments to justify its continued existence, through systems like:
The recipient of used batteries pays a bounty for them
The government (at some level) pays the company for disposal after mandating that waste be collected
The government mandates that producers pre-pay for disposal when their products are sold, also known as producer responsibility
If none of these things happen, then most often batteries just end up in the trash as is often the case in a lot of countries.
Without government support for battery recycling, which outside of the EU is relatively uncommon, then any private recycler looking to make money on recovered metals value has to effectively pay for the setup of a waste battery collection business. And if the margin on the battery isn’t enough to pay for that, then it doesn’t get recycled.
Lithium batteries occupy an interesting niche in that unlike lead-acid, NiCd or the more common MnZn alkaline batteries, they often have a significant materials value associated with them that could well justify recycling. This means that for some types of lithium batteries - lithium-ion batteries that don’t use LMO or LFP cathodes - there is not necessarily a need for the government to provide an incentive for their recycling per se. The logistics follow that.
In China, which has the best lithium battery recycling infrastructure in the world, bar none, demand pull from battery manufacturers means that there is a frenzied push for ever more collection because of all the money sloshing around chasing scarce metals for feedstock, to the extent that China pulls in materials from all over the world.
In other places, though, the feedstock collection regime is underdeveloped in part because neither governments nor private investors have been interested in recycling. That is beginning to change, but slowly. What private investors are interested in battery collection in these places often integrate the reverse logistics into their business model in order to help them make money.
There are many signs that this might be changing though. Reverse logistics for lithium batteries is likely to get a lot easier quite soon. The reason? Electric vehicles.
Not only are electric vehicle batteries just that much bigger - making it easier to get more material from the collection of a single battery - it’s very common for the manufacturers to collect the cars at end-of-life themselves. Both of these mean staggeringly lower costs of collection for the recyclers, and a much more favorable environment for them.
JUNLEE Group is an integrated full power energy factory that specializes in Uninterruptible Power Supply (UPS), Lead-Acid Battery, Battery pack, EV battery, Energy Storage Battery, Energy storage power station, Power pack Gel battery, PV Inverter and Solar system.
Production capacity reach 200000 KVaH per month. Products apply to Electric vehicles,electric mobility, solar & wind energy storage system, UPS, backup power, telecommunication, medical equipment and lighting.
JUNLEE sets up "Power research center" with more High-tech products.More than 100 engineers provided in-time and efficient one-stop solutions.
They mission strives to bring green power to the world.
To learn more about Li-ion batteries, please refer to https://www.junleepower.com/