New chemical separation technology enables recycling of batteries and biodiesel
When recycling cans and bottles, at some point it is necessary to separate plastic and metal. Extracting the most valuable metals also requires separation when recycling car batteries, but this time a special chemical separation process is required.
Cobalt, manganese and nickel found in battery cathodes are expensive to mine, and scientists have been searching for years for a way to make new batteries from used ones.
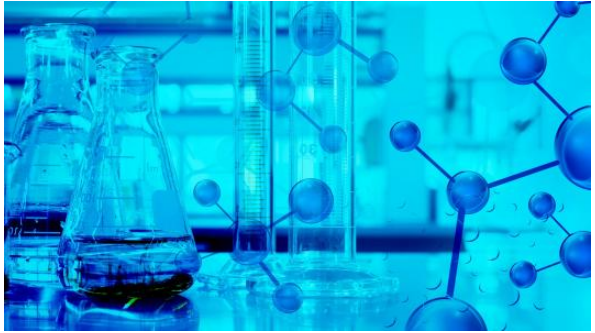
When the car's battery life reaches its limit, it is sent to an automatic shredder for shredding. Extracting useful chemicals from these shredded batteries is no easy task. Researchers at the U.S. Department of Energy's (DOE) Argonne National Laboratory have turned to a process called capacitive deionization, which uses the electrical charges of nickel, manganese and cobalt to separate them from waste streams.
Argonne engineer Lauren Valentino said: "Based on physical principles, chemical principles, as well as electrochemical principles, different separation techniques are used for different purposes. In the first step, mechanical processes can only do so much, so we turned to membranes, adsorbents as well as capacitive deionization techniques, which can be used to recapture chemicals of interest."
According to Valentino, battery recycling is very complicated because not all car batteries are the same. "When you need to recycle a car battery, it's hard to control what you get," she said. "When the battery is shredded, there's a mix of cathodes, anodes, electrolytes, separators, and so on."
Recycling batteries requires breaking down and separating large chemical components into their basic elements. “Making a battery is like building a tower out of Lego,” Valentino said. “You build a tower with small modules of different shapes, but if you want to rebuild, you have to disassemble and sort all the modules to get there. "
One of the great advantages of capacitive deionization is flexibility. According to Valentino, capacitive deionization can be adapted to a variety of materials and different operating strategies by controlling flow and operating time. "By controlling the materials and implementation, we can really customize the elements and chemicals that are separated out," she said.
The capacitive deionization process that Valtentino and her colleagues use for battery recycling also has applications in other fields, including the production of bioenergy. Valentino leads the Bioprocessing Separations Consortium, a consortium of researchers from six national laboratories working together to study and develop the separation processes and technologies needed to convert biomass into biofuels. (The consortium was formed in 2016 by the Energy Efficiency Division and Bioenergy Technologies Division of the Renewable Energy Division.)
"At some point, there's a conversion step, and then there's a separation process," Valentino said. "When these reactors produce complex mixtures with many different elements, we have to separate and concentrate what's of interest to the system, catalyze upgrades, and thus produce biological fuel."
Unlike battery recycling techniques for positively charged ions, bioenergy production requires Valentino and her colleagues to look for negatively charged molecules. Essentially, our capacitive deionization process acts like a "claw" that picks out the molecules of interest to us.
Once separated, these compounds are versatile and can be converted into hydrocarbon biofuels, such as renewable diesel or sustainable aviation fuel. "We're only just beginning to explore different ways of separating, and more efficient separation could make transportation more sustainable," Valentino said. "There's a lot more to discover."
The research was done in collaboration with NUMiX Materials and was partially funded by the National Science Foundation.
Argonne engineer Lauren Valentino said: "Based on physical principles, chemical principles, as well as electrochemical principles, different separation techniques are used for different purposes. In the first step, mechanical processes can only do so much, so we turned to membranes, adsorbents as well as capacitive deionization techniques, which can be used to recapture chemicals of interest."
According to Valentino, battery recycling is very complicated because not all car batteries are the same. "When you need to recycle a car battery, it's hard to control what you get," she said. "When the battery is shredded, there's a mix of cathodes, anodes, electrolytes, separators, and so on."
Recycling batteries requires breaking down and separating large chemical components into their basic elements. “Making a battery is like building a tower out of Lego,” Valentino said. “You build a tower with small modules of different shapes, but if you want to rebuild, you have to disassemble and sort all the modules to get there. "
One of the great advantages of capacitive deionization is flexibility. According to Valentino, capacitive deionization can be adapted to a variety of materials and different operating strategies by controlling flow and operating time. "By controlling the materials and implementation, we can really customize the elements and chemicals that are separated out," she said.
The capacitive deionization process that Valtentino and her colleagues use for battery recycling also has applications in other fields, including the production of bioenergy. Valentino leads the Bioprocessing Separations Consortium, a consortium of researchers from six national laboratories working together to study and develop the separation processes and technologies needed to convert biomass into biofuels. (The consortium was formed in 2016 by the Energy Efficiency Division and Bioenergy Technologies Division of the Renewable Energy Division.)
"At some point, there's a conversion step, and then there's a separation process," Valentino said. "When these reactors produce complex mixtures with many different elements, we have to separate and concentrate what's of interest to the system, catalyze upgrades, and thus produce biological fuel."
Unlike battery recycling techniques for positively charged ions, bioenergy production requires Valentino and her colleagues to look for negatively charged molecules. Essentially, our capacitive deionization process acts like a "claw" that picks out the molecules of interest to us.
Once separated, these compounds are versatile and can be converted into hydrocarbon biofuels, such as renewable diesel or sustainable aviation fuel. "We're only just beginning to explore different ways of separating, and more efficient separation could make transportation more sustainable," Valentino said. "There's a lot more to discover."
The research was done in collaboration with NUMiX Materials and was partially funded by the National Science Foundation.