18650 refers to the external specification of the battery, among which: 18 means the diameter is 18mm, 65 means the length is 65mm, and 0 means the cylindrical battery. Good consistency, high single energy density, good heat dissipation and other advantages. Taking the 18650 cylindrical lithium-ion battery as an example, the manufacturing process of lithium-ion batteries is revealed, and the control points of each process and its influence on the electrical performance of the battery are analyzed to provide an important reference for the application of lithium-ion batteries.
1. Lithium-ion battery
1.1 The working principle of lithium-ion battery
Lithium-ion batteries are mainly composed of a positive electrode, a negative electrode, a separator and an electrolyte, and rely on Li+ to move between the positive electrode and the negative electrode to work. During charging, Li+ is deintercalated from the positive electrode, intercalated into the negative electrode through the electrolyte, and the negative electrode is in a lithium-rich state; the opposite is true when discharging.
1.2 Lithium-ion battery structure
Lithium-ion batteries are mainly composed of four main materials: positive electrode, negative electrode, diaphragm and electrolyte. At the same time, a complete 18650 cylindrical lithium-ion battery also includes auxiliary materials such as positive and negative leads, upper and lower insulating sheets, cover plates and outer steel shells. Its structure is shown in Figure 1.
2. Manufacturing process and control points of lithium-ion battery
The manufacturing process of lithium-ion batteries is complex and there are many procedures. Errors in any link will affect the performance of lithium-ion batteries or bring about safety problems. Therefore, only by strictly controlling each manufacturing process can we manufacture products with excellent performance and safety. qualified cells. Taking the 18650 cylindrical lithium-ion battery as an example, this paper introduces the manufacturing process of the battery in detail, and explains the control points and influences of each manufacturing process.
2.1 Front-end process and control points of lithium-ion battery manufacturing
The front-end process of battery manufacturing includes 10 processes of pulping, coating, rolling, slitting, filming, winding, shelling, bottom welding, rolling groove and baking. The core of the previous process is to mix the powdered positive and negative electrodes. The material is made into a roll core.
The slurry mixing process means that the positive or negative electrode powder, the conductive agent and the adhesive are uniformly mixed into a suspension slurry in a certain proportion, and then the slurry is coated with a uniform thickness coating on the surface of the current collector through a coating machine, that is, coating process. After the coating is completed, the pole piece needs to be adjusted by the roller press to adjust the roll gap, retracting and unwinding position, tension, etc., and test the pressure with the test piece to ensure that the thickness of the test piece after the pressure test meets the requirements of the process parameters. Then use a slitter to cut into the required width of a single cell, and finally weld the tabs on the tablet machine and paste insulating glue on the tabs to cover the exposed current collectors and tabs. So far, the positive and negative electrodes are production ends.
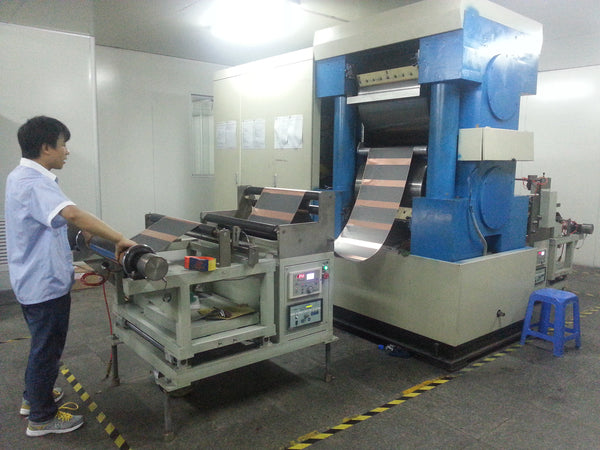
After the winding core is completed, it needs to be put into the steel shell and the negative lug is connected to the steel shell by bottom welding. At this time, the whole steel shell is the negative electrode of the battery, and then the winding core in the steel shell is fixed by the roller groove. The process of entering the shell and the roll groove can not damage the core, and the height of the roll groove needs to be strictly controlled. If it is too low, the core will be damaged; if it is too high, the core will easily loosen. Finally, the rolled core that has been put into the shell is placed in a baking oven and baked until the moisture content of the rolled core reaches the standard before it can be transferred to the next process. Baking is a crucial step in order to strictly control the moisture content of the core.
2.2 Back-end process and control points of lithium-ion battery manufacturing
The back-end process of battery manufacturing includes liquid injection, welding, sealing, cleaning and coating. Liquid injection is to inject the electrolyte into the winding core with qualified moisture requirements after baking through the liquid injection machine. After the liquid injection is completed, the four main materials of the lithium battery are all applied to the battery core. The key of the liquid injection process lies in the precise control of injection. Liquid volume, humidity control and temperature control, and waterproofing, and the effect that the electrolyte can infiltrate into the positive and negative pole pieces well must be achieved. The amount of electrolyte is directly related to the safety performance and capacity of the battery. If the amount of liquid injection is too large, the gas production inside the battery will be large, and the safety valve of the cylindrical battery will often open prematurely; if the amount of liquid injection is too small, the battery capacity will be reduced. It will be low and lithium will be precipitated, which is more likely to cause thermal runaway or even cause an explosion. Then weld the cover plate and the positive lug together. At this time, the entire cover plate is the positive electrode of the battery. The welding control point is to prevent false welding, partial welding and poor appearance of the cap.
The next process is sealing. Sealing is to seal the steel shell and the cover plate, and isolate the entire coil core from the external environment. The entire coil core is a closed electrochemical system. The sealing process is the last crucial process in the manufacture of the entire battery cell, and the process stability of its pressure forming technology determines whether the sealing performance of the battery is complete and reliable. Completing the sealing process means that the manufacture of a complete battery cell has been completed. The purpose of the cleaning process is to remove the residual electrolyte on the surface of the battery steel shell to prevent the electrolyte from corroding the steel shell, while the coating process is to ensure the separation of the positive and negative poles of the battery cells to prevent short circuits in external circuits, and at the same time to make the battery have a certain aesthetics, These two processes also require screening of batteries with poor appearance.
2.3 Li-ion battery screening process and control points
Due to differences in battery raw materials and production processes, there are differences in battery capacity, voltage, internal resistance and other properties, so that the performance of the battery pack cannot reach the level of single cells, and the service life is much shorter than that of single cells, which affects the use of electric vehicles. The battery screening process includes activation, formation, aging, sorting and capacity separation.
The activation process is that after the cell is covered with a membrane, it is put on hold for a period of time in a constant temperature environment, so that the electrolyte can fully infiltrate the pole pieces and diaphragms to prevent lithium precipitation due to uneven infiltration of the electrolyte. The formation process is the first charging of the lithium-ion battery. This step promotes the formation of a "solid electrolyte interface film" (SEI film) on the surface of the electrode, which means that the electrolyte is decomposed by redox during the first charging process of the lithium-ion battery. The interface film formed on the surface of the electrode material has the characteristics of ion conduction and electronic insulation. Li+ can be freely embedded and extracted through the film. Because of the characteristics of solid electrolyte, it is called "solid electrolyte interface film".
SEI film is the guarantee condition for the long-term stable operation of lithium-ion batteries, which has a crucial impact on its capacity, rate, cycle, and safety performance. Selecting the appropriate formation current, formation voltage, formation temperature, etc., plays a very important role in optimizing and improving the battery performance, so this process is very important. In the actual operation process, it is necessary to prevent the battery from reverse connection, overcharge and poor contact.
The aging process is to put the cells in a certain state of charge in a certain constant temperature environment for a period of time, and screen the data through the voltage before and after the test, and eliminate the cells with large voltage drop or abnormal voltage drop. Generally, when a micro-short circuit occurs inside the cell or there is a severe side reaction, the voltage drop of the cell will be large, reflecting that the poor performance of the cell will have certain safety risks. Therefore, the voltage drop is one of the important reference indicators for cell selection.
Due to the long aging time at room temperature, in order to shorten the production cycle, most lithium-ion battery manufacturers adopt the aging method of high temperature or high state of charge. To ensure safety, because the general high-temperature aging room is a closed space, it is not easy to be discovered in time at the initial stage, and once a fire occurs, the consequences will be disastrous.
The sorting process is to sort the cells with different internal resistance gears according to the AC internal resistance of the cells, and eliminate the abnormal cells with internal resistance. One of the reference indicators.
The capacity dividing process is to measure the capacity of the battery cells and screen the batteries according to different capacity gears, and remove the unqualified batteries. Due to the large relationship between the capacity and the temperature, the more accurate the environmental temperature control during capacity dividing, the closer the capacity is to the real value, the higher the capacity. Bit allocation is more accurate, therefore, temperature control is the key point of capacity control. The shipped cells must be qualified cells that have been screened for voltage drop, internal resistance and capacity.