Computed tomography (CT) technology is mainly used in the medical field to detect the internal health status of the human body. With the development of related technologies, especially the resolution of radiation sources and detection devices, micron-scale X-ray computed tomography technology is gradually applied in the fields of geological exploration, bionics and materials science.
By comprehensively scanning the internal structure of the test sample, tomographic images with different contrasts are formed according to the density difference of the internal structure, so as to accurately grasp the number, volume fraction and distribution of pores, inclusions, cracks and the three-dimensional space of the material microstructure inside the sample It is helpful to analyze the relationship between defect information and mechanical properties of materials, identify the role of defects in material failure, and then help to study the failure mechanism to optimize and improve the material preparation process.
This paper analyzes the internal structure characteristics of lithium-ion power battery cells through computer tomography technology, aiming at the battery life and safety issues that are closely concerned by the current lithium-ion power battery industry. In terms of battery aging degree, the evolution of the overall internal structure of the battery after different cycles is compared in detail; in terms of battery safety hazards, problems such as electrode fracture, electrode folds, pole piece alignment and internal foreign matter are analyzed in the computed tomography images. The characteristics of the battery were analyzed, and the internal structure of the battery after the safety test was analyzed.
1. Test methods and technical parameters
1.1 Test method
Figure 1 is an X-ray computed tomography test photograph. The left side is the X-ray source, the middle is the test sample stage, and the right side is the detector. These three key components are located inside the shielded lead room to ensure that the test personnel will not be affected by X-ray radiation during the test.
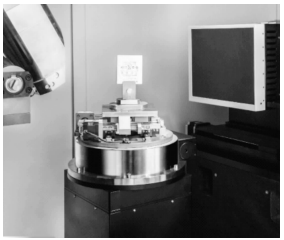
The X-ray tomography analysis performed in this paper was performed using a nanoVoxel-4000 computed tomography system from Tianjin Sanying Precision Instrument Co., Ltd. During the test, the X-ray source voltage was set to 225kV, the resolution was 2μm; the imaging area of the X-ray detector was 244mm×196mm, and the imaging range was 300mm×450mm (diameter×height). The experimental conditions of X-ray computed tomography test are shown in Table 1.
2.1 Non-destructive testing of power battery cell aging degree
In order to explore the evolution of the internal structure of the power battery after long-term cycling, the 1# sample was charged and discharged at a rate of 2C, and the test was suspended after a certain number of cycles, and the battery was discharged to empty electricity. , analyze the changes in its internal structure. Figure 3 is a computed tomography longitudinal section image of the test sample. Figures 3(a)–(d) correspond to new batteries with cycles of 500, 1000, and 2000 cycles, respectively. The internal structure of the battery that has not been cycled is very regular (Fig. 3(a)), and a layered wound electrode and a void in the center of the battery can be observed. When the cycle was up to 500 cycles (Fig. 3(b)), it could be observed that the internal electrode had obvious bulges, and the bulges were mainly concentrated at the bottom of the battery. When the cycle reached 1000 cycles, bulges appeared on the bottom and upper ends of one electrode. When the cycle reached 2000 cycles, the bulges on one side were connected together, forming larger bulges and smaller bulges on the other side of the electrode. rise.
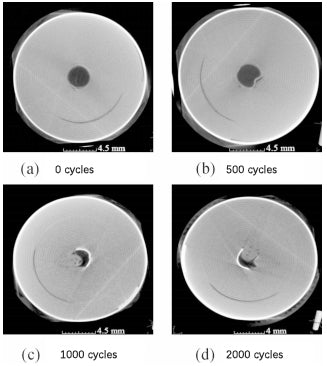
2,2.1 Structural fracture
The power battery will break the electrode structure due to factory defects or the charging and discharging process. The fracture of the electrode generally occurs at the bending point of the internal electrode of the battery, such as the inner side of the coiled cell of a cylindrical battery, and the inner side of the coiled and stacked electrodes of a soft pack and square case battery. Figure 5 is a CT scan image of the internal electrodes of a rectangular hard case battery. A clear layered structure of positive and negative electrodes can be observed from Figure 5(a) and (b), the layer with high contrast corresponds to the positive pole piece, and the layer with low contrast corresponds to the negative pole piece.
2.2.2 Electrode pleats
In the power battery, whether the electrodes are wrinkled can represent the overall regularity of the internal structure of the battery, which is related to the degree of ex-factory of the battery and the degree of use of the battery. Figure 6(a) and Figure 6(b) are the results of CT scanning on two square hard-shell batteries of the same type. It can be observed that in Fig. 6(a), each layer of the electrode in the flat and curved area shows high consistency, and the void in the center of the battery winding also presents a straight line with a high degree of regularity; from Fig. 6( b) It can be clearly observed that some electrodes are wrinkled, and the electrodes are bent as a whole.
2.2.3 Pole piece alignment
The difference in the alignment of the pole pieces of the battery is mainly caused by the process level of the battery when it leaves the factory. Poorly aligned pole pieces can lead to asymmetry between the positive and negative electrodes, which not only results in partial capacity loss, but also increases the risk of internal short circuits in the battery. For example, when scanning multiple square shell batteries of the same model, the electrode areas with different alignments are shown in Figure 7.
2.2.4 Foreign objects in the battery
The foreign matter inside the battery is mainly caused by the process defects of the battery when it leaves the factory. Since CT scanning technology is sensitive to high-density materials, it is mainly metal foreign objects that can be detected. As shown in Figure 8, the metal foreign matter detected in Figure 8(a) is a metal foreign matter in the electrode. A high-contrast spot with a particle size of about 100 μm × 200 μm can be observed in the electrode, which is located between the two layers of electrodes in the battery. As shown by the arrow in the figure. The foreign matter in the electrode is likely to cause the temperature of the micro area to be too high during the use of the battery, resulting in a safety hazard. Figure 8(b) is an image of foreign matter in the battery sealing ring, and the particle size of the foreign matter is about 100 μm. Foreign matter in the sealing ring may cause the battery to be loosely sealed and cause the hidden danger of electrolyte leakage during use.
2.3.1 Electrical safety test
Figure 9 shows the CT images of a certain 18650 battery before and after the overdischarge test. Figure 9(a) is the cross-sectional and longitudinal cross-sectional images of an empty battery that has not been over-discharged. It can be observed that the inside of the battery presents a regular winding structure of positive and negative electrodes. Figure 9(b) shows the battery after 1C overdischarge to 150% DOD, and after 1 charge-discharge to empty. From the CT image, it can be observed that the overall winding structure of the battery remains relatively intact, but small burrs can be seen, which is caused by the copper dissolution of the positive electrode during the overdischarge process of the battery. In addition, by measuring the thickness of the positive and negative electrodes, it was found that after the discharge, the thickness of the positive electrode increased from 102.7 μm to 182.1 μm, and the thickness of the negative electrode increased from 175.2 μm to 198.6 μm, indicating that the electrode thickened during the overdischarge process.