In terms of battery pack thermal management, we propose a method to quickly estimate the flow field and temperature field inside a parallel air-cooled battery pack. The method consists of a flow resistance network model and a transient heat transfer model, which avoids the problem of excessive computational complexity when the computational fluid dynamics method is used to simulate large battery packs, while ensuring high estimation accuracy. Using this method, we investigated the effect of uneven flow field on the temperature uniformity in the battery pack, and with the goal of improving the temperature uniformity, the structural parameters of the air-cooling system were discussed, and a feasible parameter configuration was given. Program.
Due to differences in the parameter values of voltage, internal resistance, capacity, etc. of the same type and specification of batteries, when they are used in electric vehicles, their performance indicators often cannot reach the original level of single batteries, which seriously affects their performance in electric vehicles. applications in automobiles.
Consistency of lithium-ion batteries refers to the consistency of initial performance indicators of single cells used in groups, including: capacity, impedance, electrical characteristics of electrodes, electrical connection, temperature characteristics, decay speed, etc. The inconsistency of the above factors will directly affect the difference of output electrical parameters during operation.
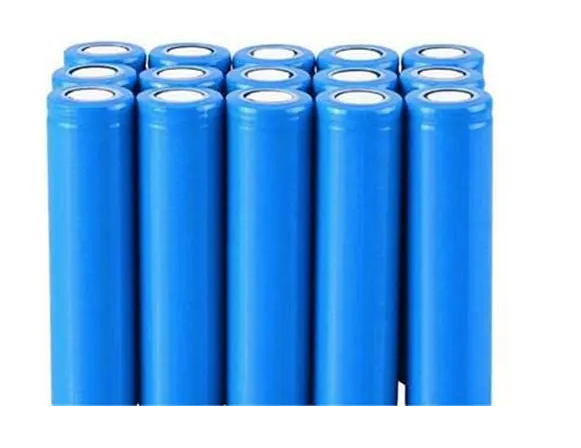
The inconsistency of the lithium-ion battery pack or the discrete phenomenon of the battery pack refers to the voltage, charge, capacity, decay rate, internal resistance and its rate of change with time, life, temperature, impact, self-discharge rate and its rate of change over time.
After the single battery is manufactured, there are certain performance differences. The initial inconsistency accumulates with the continuous charging and discharging cycles of the battery during use, resulting in greater differences in the state (SOC, voltage, etc.) of each single cell; all the same. This causes the inconsistency of the single cells to gradually enlarge during use, which in some cases accelerates the degradation of the performance of some single cells, and eventually leads to premature failure of the battery pack.
The reasons for the inconsistency are divided into chronological order. The inconsistency of the single cells in the battery pack is mainly reflected in two aspects: the process problems in the manufacturing process and the non-uniformity of the materials, which make the activation degree and thickness of the active materials of the battery plates and the micropores. There are very small differences in the rate, connecting strips, separators, etc., resulting in incomplete consistency in internal structure and material; when loading and using, the electrolyte density, temperature and ventilation conditions of each battery in the battery pack, and the degree of self-discharge and the impact of differences in the charging and discharging process.
Analysis of the differences in the capacity, internal resistance and self-discharge of the same type of battery from the same batch
In view of the reasons for these inconsistencies, whether it is possible to completely eliminate the inconsistencies in the battery pack through some measures: Many people think that the inconsistencies of the batteries are a problem of the production process, and some people think that it is a problem of the matching process. Process control measures such as SPC can be used. Completely eliminate battery inconsistencies.
However, practice has proved that even if the process of batching, live pulp, coating, cutting, rolling and other processes is strictly controlled, it can only reduce the standard deviation between batches of products, but cannot eliminate inconsistencies. If there are many random factors affecting a random variable, and the influence of each factor alone cannot play a decisive role, and the influence of these factors can be superimposed, the random variable obeys a normal distribution, and the characteristic parameters have standard deviation σ and mean μ. The voltage value of the battery charging and discharging process is a comprehensive reflection of the thermodynamic and kinetic state of the battery, which is not only affected by the process conditions of each process in the battery production process, but also affected by the current, temperature, time and accidental factors during the battery charging and discharging process. Therefore, the voltage value of each battery in the battery pack cannot be exactly the same.
Improvement measures
1. Production process measures Battery companies control the consistency of various raw materials; monitor the rheology of the slurry, do not leave the slurry for a long time to ensure that the rheology of the slurry is the same during coating; monitor coating parameters, especially Lithium iron phosphate slurry, due to the finer particles of lithium iron phosphate, the processing performance of the slurry is poor, attention should be paid to slow down the speed of the coating machine during coating; reasonable detection of slurry viscosity; visual inspection of the pole piece; Defective pole pieces; pole piece weighing; comparison of battery quality before and after liquid injection; formation temperature; humidity control; formulate standards for various raw materials, and inspect and store raw materials in strict accordance with the standards; control the consistency of production processes; The consistency of the production process is finely regulated; the process is subject to strict statistical process control (SPC); each process is ensured within the specified tolerance range; the process capability index is ensured to follow the normal production parameter distribution law.
2. The measures in the grouping process ensure that the battery pack adopts batteries of uniform specifications and models, and ensures the consistency of the quality of the batteries, especially the initial voltage. Screening conditions: voltage; internal resistance; battery formation data; there are many consistency evaluation methods. The most commonly used are the range coefficient method, the standard deviation coefficient method and the threshold method. Combined with cluster analysis, the shape, distance, and area of the battery charge-discharge curve formed by each detection point within the set time interval are used for scientific classification, so as to determine the consistency of the battery. On the basis of the capacity or voltage threshold, the shape of the charge-discharge curve, the distance between the curves, the area enclosed by the curve, etc. are calculated, and the parameters that can reflect the consistency of the curve are selected for judgment. During the charging and discharging process, the curves are close, the relative distance is small, the area enclosed by the curve is small, and the cells with small differences between groups are matched, so as to achieve the optimal consistent grouping.
3. Battery balance management From the perspective of the battery management system, the parameters of the single cells are detected during the use of the battery pack, especially the voltage distribution during the stop or driving of the electric vehicle, and the development law of the inconsistency of the single cells in the battery pack is grasped. The battery should be adjusted or replaced in time to ensure that the parameter inconsistency of the battery pack does not increase with the use time. Avoid overcharging the battery and try to prevent the battery from deep discharge. Ensure a good operating environment for the battery pack, try to maintain a constant temperature, reduce vibration, and ensure that water, dust, etc. contaminate the battery pole. At the same time, from the perspective of energy management and strategy, a practical battery pack energy management and balancing system is introduced to formulate a reasonable battery balancing strategy to actively intervene and reduce battery inconsistency.