Fast charging is to allow more power to be charged into the battery from the grid. If this problem is to be broken down, several links are needed:
Grid->Charging pile/device->Battery (Pack)->Battery (Cell)
Then we can split these links and analyze them one by one: This article focuses on the most challenging Fast charging of electric vehicle batteries has only a few incidental introductions to mobile phones and electric bicycles.
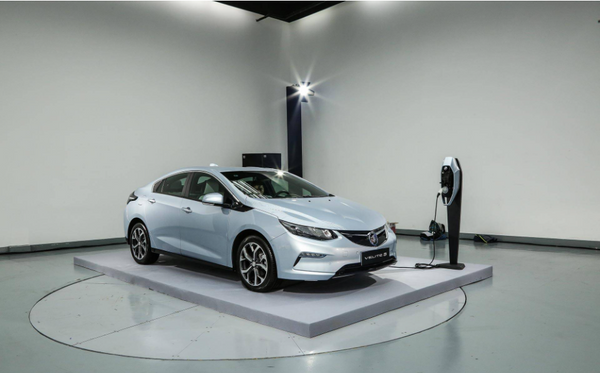
(1) Power grid
If you have some basic understanding of the power grid, everyone will know that the power grid actually needs to generate and use electricity immediately, and balance the power all the time. Therefore, power generation/power consumption should be matched at all times as much as possible, and rapid changes in power consumption in a short period of time will bring challenges to the transmission and distribution links. For fast charging, this means that we can do work in the following aspects:
Power generation side: add flexible units (flexible transformation of coal power to improve climbing ability, and introduce more flexible but high-cost gas turbine units) to improve the ability to respond to power changes. Transmission and distribution side: mainly increase power supply capacity and allow transmission power to go online (Simply put, use a thicker wire that can send more current...)
Electricity side: In fact, a simple solution is to increase resources in the fast charging station. For example, if you put a battery pack to make a large power bank, you can carry out the battery (power bank) -> energy transmission in the car battery. It will not have a relatively large impact on the overall operation of the power grid. Or a local photovoltaic power plant/distributed fuel cell power plant is working. Generally speaking, it is: to improve the instantaneous energy supply capacity, and prepare the transmission capacity (wires) required for power transmission and distribution. And if it is only for the fast charging of small batteries such as mobile phones, the impact on the power grid is basically zero; for electric bicycles, it is mainly some adjustments in the safety of transmission and distribution. This power has a small impact on the large power grid. .
(2)Charging pile
The main influencing factors of the charging pile are the capacity limitation of the DC/AC pile, the interaction between the charging pile and the battery pack, and the 400V/800V technical route. The capacity limitation of the DC/AC pile: currently for electric vehicles, generally low power It is AC AC pile (<20kW), high power is DC DC pile (mostly >20kW, for example, CHAdeMO is 50kW, Tesla's super charge is 120kW). AC piles and DC piles generally need to be designed accordingly to meet a certain voltage-current delivery capacity. In 2017, Porsche has launched a 350kW DC pile, which can be matched with its recently launched Taycan and Audi e-tron to meet the 3C rate of the battery pack of about 100kWh (corresponding to about 20 minutes) fast charge charging pile and battery Group interaction: For DC/AC piles, both the power transmission interface and the communication interface have certain standards to accurately connect with the vehicle, and real-time grasp of the vehicle's situation for power transmission. Therefore, as many answers have said, it is not that the 50kW charging pile means that he has been charging the car with 50kW, but this is only the maximum capacity. The power is always changing during actual fast charging, which mainly depends on the grid. The energy supply at that time and more importantly: the real-time situation of the electric vehicle battery (group), it will return a signal to the charging pile through communication, and the two sides will dynamically cooperate with the influence of the 400V/800V technical route: everyone knows that P=U* I, for high power, either increase the current or increase the voltage. The current AC AC pile and DC DC pile are basically 400V, and if the charging power is further increased, this will result in a very large maximum current -> a very thick wire is required. Therefore, in the next development process, increasing the fast charge to 800V is a recognized next step.
Of course, this is not an easy task, high voltage will bring a series of corresponding upgrades such as insulation standards, and the charging pile must also be considered in this regard. Especially for the >100kW fast charging technology (Porsche 350kW) that everyone is currently developing, going to 800V is the general trend. Of course, it also requires the cooperation of the battery pack system.
3) Battery system
The main considerations are the impact of 400V->800V high voltage, thermal management and the communication interaction between BMS and charging pile. The impact of 400V->800V high voltage: A car is composed of multiple cells in series and parallel to form a battery pack/battery. At present, almost all electric vehicles use 400V working voltage. This can be a good match with the charging pile. However, with the development of fast charging, 400V fast charging also has a bottleneck in the battery system: too much current inevitably requires a stronger current-carrying capacity of the current collector, but the battery pack needs to be lighter and smaller, and it is impossible to be unlimited Use thicker/more expensive busbars with lower resistance, so 800V battery pack technology (future direction) must be developed to match the 800V fast charging technology of charging piles. The internal design of some battery packs of TAYCAN, the first 800V battery system electric vehicle launched by PORSCHE. Of course, 800V battery pack technology also has its own challenges. One of the core issues is that the high-voltage insulation protection level of the battery system/vehicle needs to be improved accordingly.
Thermal management: There are often hundreds to thousands of battery cells in the car battery system. During operation/charging, the temperature of each battery cell in the battery system is often uneven, which will result in different battery cells. The charging/discharging capacity is obviously different, which may lead to acceleration of attenuation (see NISSAN LEAF of air cooling), or cause partial over-discharge and over-charge, leading to thermal runaway, thermal diffusion, and eventual development of accidents. For example, the following figure shows two examples of poor and good thermal management effects. In addition, the fast charging capacity of the battery cell material also depends on the temperature: when the temperature is too low, the maximum allowable charging current is also low, so a certain heating of the battery core during fast charging is a preparation condition for fast charging. When the temperature is too high, taking into account the thermal effect of charging, fast charging will also aggravate the aging of the battery cell. Therefore, a thermal management system is required to ensure that the battery cell is within a reasonable temperature range, which is not too high or not too low. Therefore, in general, for higher energy density ternary battery packs + higher power charging, typical thermal management such as liquid cooling + cold plate is basically standard, and those that do not require liquid cooling are generally lithium iron phosphate/ With a ternary system with low energy density, it is difficult for the overall market positioning of a car with such a battery configuration to enter the middle and high-end.
Communication and interaction between BMS and charging pile: BMS is Battery Management System, which collects and monitors various information such as battery cells/modules' electricity/temperature in real time; in the actual charging process, BMS collects various information of incoming cells and analyzes them , Interact with the charging wizard to ensure that the charging power is still within the working window range that the battery cell can handle.
(4)Battery cell
There are a lot of answers and documents about the battery cell's fast charging capability. Here I want to make three points: all battery cells have their own fast charging capability. Its own mechanism, as well as the coordination of the various materials of the battery as a device (barrel effect, the shortest determines the upper limit of fast charging capacity) All batteries have their own fast charging capacity: in fact, all batteries can be compared to it The ability to charge and discharge at a larger current at a rated power, such as the charge and discharge curve extracted from the figure below (haha, a copy of the original Dr. Liu). The solid line is the low rate charge and discharge curve, and the dashed line is the high rate charge and discharge curve. . The faster charging/power capability is stronger, the closer the high-rate charge-discharge curve is to the low-rate charge and discharge curve, and vice versa. Therefore, it is not difficult to see that batteries are different from batteries. Therefore, for each battery cell, the voltage and current range suitable for work must be determined according to its performance, recorded and managed by BMS, so in fact, what everyone sees The battery can only be charged and discharged at a fixed rate. Why? Because all are defined for you in accordance with the industrial development process, this is the result of compromise after considering various factors in engineering development. The mechanism of fast charging itself: specifically implemented on a single battery cell, fast charging will only be implemented in 5V-high current input (even if it is 9V fast charging on a mobile phone, it must be converted to 5V at the end), mainly for fast charging The part of the charge is the CC FAST CHARGE segment in the middle of the battery (fast charge is especially unlikely to occur at the end of the charge because of lithium Li-plating).
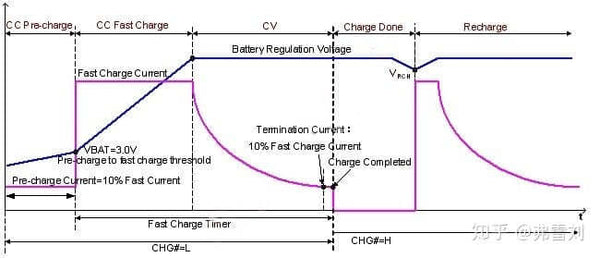
Then it depends on the coordination of the various materials in the battery. The coordination of various materials in the battery: A battery is also a device, and all parts of it must be well matched to have the final good fast charging performance. The positive electrode, negative electrode, separator, electrolyte, and current collector all need to be coordinated. It is necessary to have a higher conductivity/multiplier performance as much as possible, and at the same time to minimize occupying more mass and volume (increase in energy density generally inevitably leads to faster charging. It is difficult, so who can achieve both fast charging and energy density is the skill), and the design of the cell structure is also very important. Therefore, as a whole battery, the components must be closely matched, not a single material with a single performance.
->Therefore, many documents are aimed at the optimization of fast charging under specific conditions of a material. In fact, it is a very partial research idea. Looking at the industry, the work is of course very academically meaningful, but the limitations are too large. In the actual battery cell technology, in fact, the shortcomings of the final fast charging are almost all currently in the lithium-plating of the graphite anode material, which will cause the precipitation of lithium dendrites, which may pierce the diaphragm, and finally Cause a thermal runaway accident of the lithium battery. Under the two conditions of the end of charging and low temperature, the risk of lithium evolution will increase sharply, so this is also the most challenging condition for fast charging.
So in the end, it must be emphasized that the negative electrode lithium is the bottleneck, it is the bottleneck, it is the bottleneck. It is not easy to balance the energy density and fast charging capacity of the battery cell design. This is the core Know-how of the battery cell factory. It is also the most challenging point among the fast charging factors mentioned above (personal opinion for discussion). Someone still wants to ask if the battery will be damaged if it is quickly charged. The conclusion is: it must be damaged, but the degree of damage varies depending on the battery. If the fast charge performance is good + the use environment is mild, the damage caused can be as small as possible or even close to zero; if the fast charge performance is not good + the use environment is not good It's troublesome. Frequent use will inevitably cause rapid aging and failure.
In the future, JUNLEE Energy, which has been committed to battery research and development, is a challenge and an opportunity. The R&D team of engineers will provide the world with more economical new energy batteries, and will improve lithium-ion battery technology to reduce the total cost.
JUNLEE Group is an integrated full power energy factory that specializes in Uninterruptible Power Supply (UPS), Lead-Acid Battery, Battery pack, EV battery, Energy Storage Battery, Energy storage power station, Power pack Gel battery, PV Inverter and Solar system.
Production capacity reach 200000 KVaH per month. Products apply to Electric vehicles,electric mobility, solar & wind energy storage system, UPS, backup power, telecommunication, medical equipment and lighting.
JUNLEE sets up "Power research center" with more High-tech products.More than 100 engineers provided in-time and efficient one-stop solutions.
They mission strives to bring green power to the world.
To learn more about Li-ion batteries, please refer to https://www.junleepower.com/