Asahi Kasei's first practical Li-ion battery (LIB) prototype was fabricated in 1985 under the direction of Dr. Akira Yoshino, with the most notable innovation being a high-performance separator that was designed to enable lithium A very important factor in the safety performance required for the commercialization of ion batteries.
The separator is one of the most important components in a lithium-ion battery. Located between the anode and cathode of the battery, it prevents physical contact between the electrodes, while the separator facilitates the transfer of ions in the battery. Diaphragm failure can cause a short circuit in the battery, causing thermal runaway.
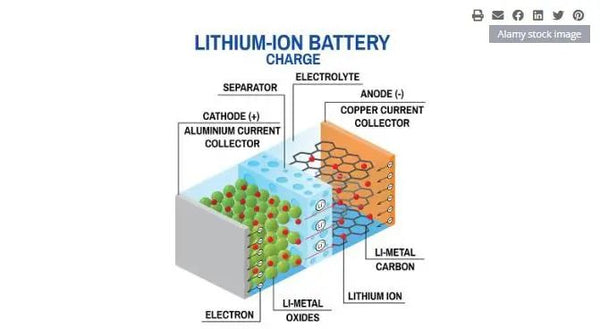
• High electrolyte absorption
• Be as thin as possible without adding unwanted bulk
• Chemical and electrochemical stability
• Appropriate level of uniform porosity
• Wetting
• Appropriate impedance
• Optimum cycle life
Balancing all of the above characteristics to create a technology that is not only safe, efficient, but also cost-effective is a huge challenge. Here are some of the different technologies in the lithium-ion battery separator market at this stage:
Celgard: One of the solutions for battery electric vehicle applications involves the use of a polypropylene/polyethylene/polypropylene (PP/PE/PP) three-layer structure. The polypropylene outer layer not only provides high temperature melt integrity (HTMI), a critical property for safety, but also provides oxidation resistance. Polyethylene inner layer can be quickly closed during thermal runaway.
Celgard H1809 consists of an 18-micron triple-layer microporous membrane (PP/PE/PP) with a porosity of 49%. The H1809 is designed for use in high energy lithium battery systems; especially those devices that require special safety and energy density advantages.
UBE: Among the solutions for automotive applications, there is an option for a ceramic-coated diaphragm called CPORE. CPORE is a high performance separator coating made using advanced dispersion technology and high speed and precise coating on the separator surface.
CPORE thicknesses range from 13 to 25 microns. Inorganic particles are used in these separators to further improve their heat resistance, minimize shrinkage caused by abnormal heating, and prevent short circuits inside the battery, significantly improving the safety of lithium-ion batteries.
Entek: Entek offers coated and uncoated separators based on Ultra High Molecular Weight Polyethylene (UHMWPE). One of the products, EPH, targets high discharge/charge rate applications in portable electronic devices, such as cordless power tools, lawn and garden equipment, high-power remote-controlled cars, and more. The thickness of the EPH separator ranges from 9 to 16 microns and the porosity is 48%.
Soteria: Soteria's patented technology purportedly eliminates the root cause of thermal runaway, isolates short circuits, and allows batteries to continue to function after damage. Soteria's non-woven membranes are reinforced with aramid fibers, creating a membrane that won't melt or shrink in the presence of defects or damage. In addition, the metallized film current collector blows like a fuse, isolating the short circuit and the rest of the battery can continue to operate.
Separators contribute to the safety and reliability of lithium-ion batteries. Although lithium-ion batteries are challenging to innovate and commercialize, research and development efforts are still very active. According to Graphical Research, the compound annual growth rate (CAGR) of lithium-ion battery separators in North America is likely to reach 16.2% by 2027. The battery separator roadmap looks very promising, and there are also safer and better innovations.